For decades, our authentic peacoat has been made from a woolen cloth, a blend of virgin and recycled wool. This woollen cloth has been made for over 150 years by an exceptional French company, "Entreprise du Patrimoine Vivant".
This woolen cloth allows our peacoat to be water-repellent and breathable while retaining body heat and eliminating perspiration. Its insulating properties make it effective against cold and wind, while its breathability helps wick away moisture.
Our real peacoat is navy. A symbol of our maritime heritage, this is the original colour of the peacoat, reflecting its history and authenticity. In the past, it had the advantage of better camouflaging the stains associated with working at sea. Today, navy blue embodies both elegance and tradition.
Originally, the authentic peacoat had a straight and short cut to facilitate the movements of sailors. Today, a true everyday partner, our peacoat is available in different cuts: straight, fitted or fitted with a martingale. These cuts make it possible to adapt to the styles and morphologies of each one.
Step 1 Dyeing the raw material
Our French woollen cloth is made from a blend of virgin and recycled wool. In the first stage, the unbleached virgin wool is dyed navy. The recycled wool is already dyed, as it comes exclusively from sailor sweater cuttings.
Step 2 Preparation and mixing
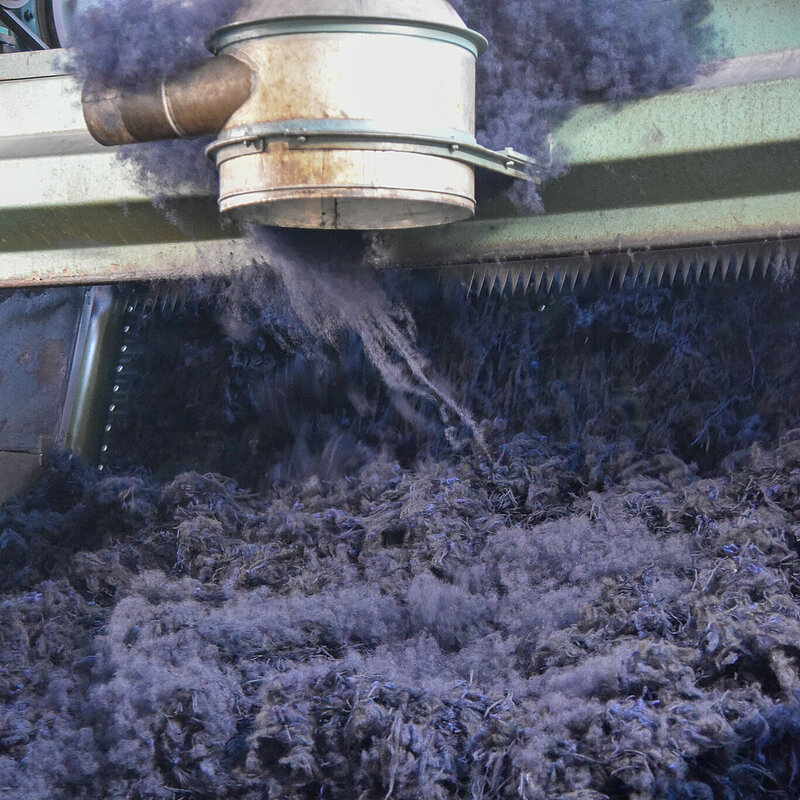
Once the dyeing has been completed, the two types of wool must be prepared and mixed. This mixture of several shades of blue and black will add depth to the final color of the wool cloth.
Step 3 Carded spinning
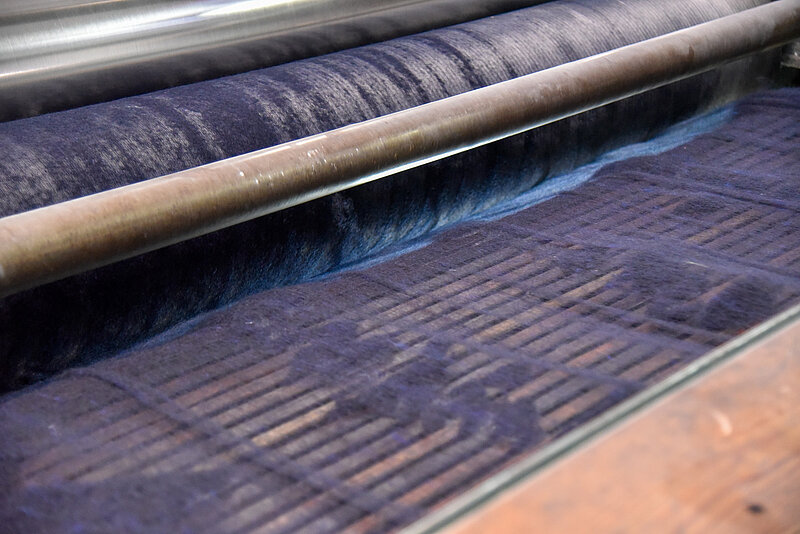
At this stage, the wool fibers are combed and untangled using carding machines, special combs with metal teeth. Carding cleans and aligns the fibers in the same direction. The sliver is then spun into a continuous yarn. This is carded spinning.
Step 4 Weaving
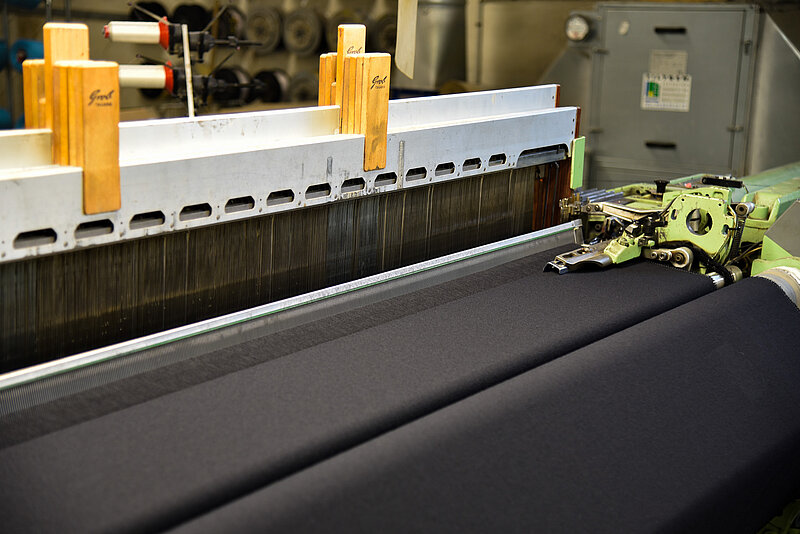
Next comes the weaving stage. For this stage, the wool yarns are connected to a loom, a machine used in the textile industry. A distinction is made here between two sets of threads: warp and weft. The weft threads pass alternately over and under the warp threads to form large pieces of fabric.
Step 5 Wool washing and fulling
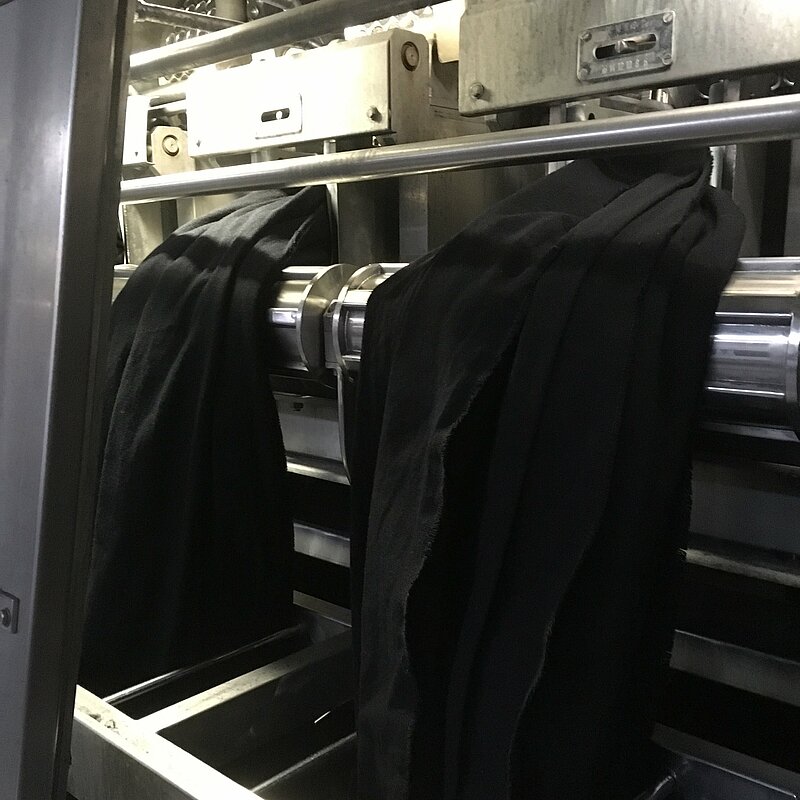
To become a woollen sheet, woollen fabrics must then undergo fulling. This stage felts the fabric using a mechanical process. Placed in a vat filled with hot water and soap, the fabric is struck repeatedly by fullers (mechanical beaters). This step ensures effective interlacing of the wool fibers, giving the fabric exceptional thickness, abrasion resistance and durability.
Step 6 Dry finishing
During this final stage, the wool cloth undergoes ennobling, a set of processes and techniques designed to improve its characteristics. Here, the wool cloth is subjected to a thermal shock under several bars of pressure. It becomes water-repellent and virtually indestructible. At this stage, the wool cloth undergoes an anti-pilling treatment to give it a firmer hand.